Custom battery packs are tailored to specific product applications, such as size constraints, unique shapes, or specific functional requirements. This custom design provides a significant competitive edge in the market.
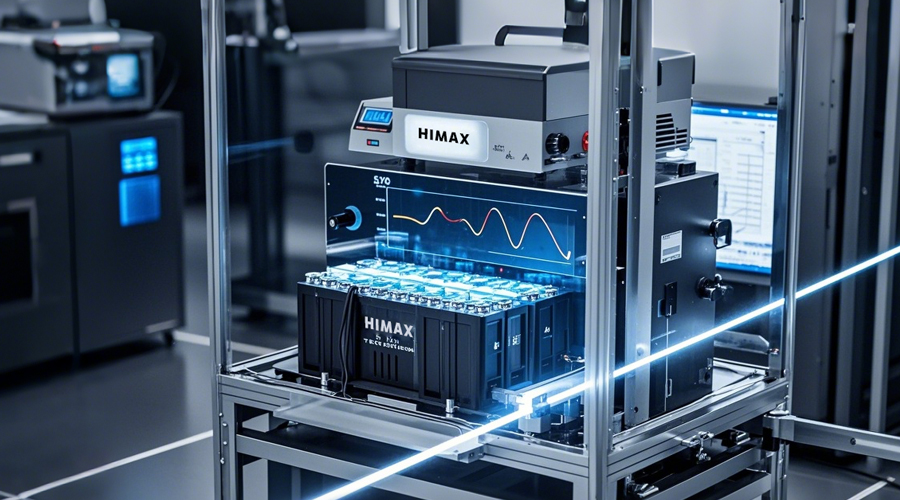
Our engineers focus on solving key challenges for customers, such as voltage, capacity, and current, while designing the most suitable battery solutions based on the product’s actual needs. They also consider which cell specifications best meet the required dimensions and power consumption, always aiming for the best cost-performance ratio.
Custom Battery Solutions by Himax Battery Factory
Himax Battery Factory has successfully designed various custom battery solutions based on customer needs, including:
· 22.2V cylindrical battery pack for underwater monitoring
· 76.8V 480Ah large capacity battery for golf carts
· 12V 2.2Ah high-temperature AA battery for specialized applications
These custom solutions perfectly meet our customers’ needs, ensuring both product performance and reliability.
How to Handle Design Requests That Do Not Meet Battery Performance Standards?
If a customer’s requested design conflicts with the standard battery performance specifications, we follow a systematic process to find the best solution:
- Thoroughly Understand Customer Needs: We gain a full understanding of the customer’s application, environment, and use case to ensure our solutions are practical.
- Explain Design Limitations and Optimize Solutions: We explain why certain design elements may not be feasible and propose the best alternative solutions.
- Verify Feasibility: We validate the proposed solution and send the data to the customer for confirmation.
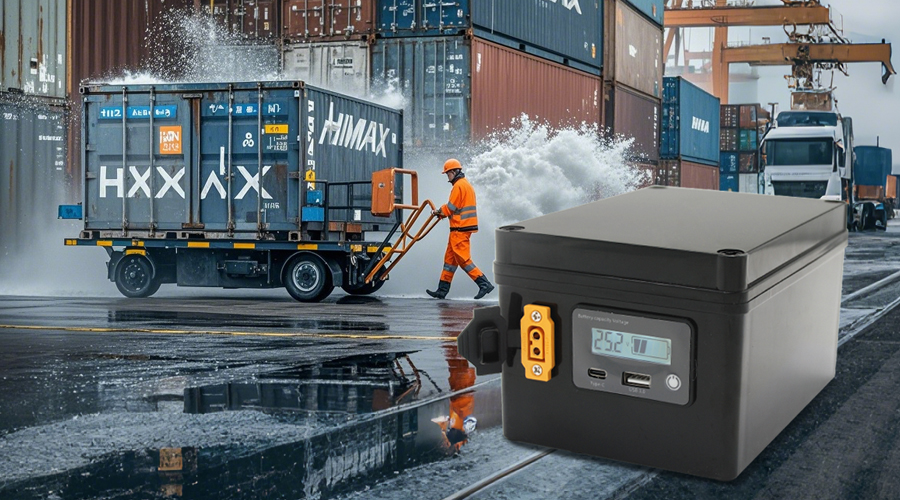
Example: Custom Battery Pack Design for a French Customer – 25.2V 10Ah Battery Pack
For example, a French customer requested a 25.2V 10Ah lithium battery pack for a trolley. They wanted the battery pack to include a display and a step-down module, so they could monitor the battery’s status in real-time.
Considering the extended shipping time to Europe (typically 30 days or more by sea), we recommended adding a switch between the step-down module and the protection board to disconnect the power consumption, thus minimizing battery discharge during shipping.
Why Was This Necessary?
Let’s calculate the battery consumption during the one-month shipping period:
· Our factory ships lithium battery packs with a 30% charge (i.e., 3Ah for the 25.2V 10Ah pack). The self-discharge rate of lithium batteries is typically less than 3% per month. At a maximum self-discharge rate of 3%, the battery will lose 0.09Ah, leaving 2.91Ah upon arrival.
· The step-down module consumes 15mA per hour, totaling 10.8Ah per month, which means the battery would be completely drained.
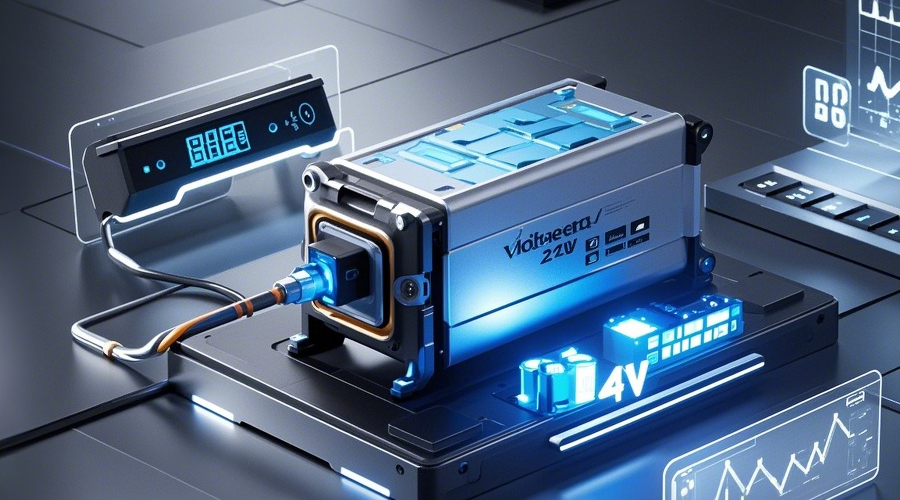
· Additionally, the display consumes 30uA per hour, adding 21mAh per month.
Combining all the calculations, the battery will be completely drained upon arrival, making it unusable unless recharged.
Consequences of Depleted Batteries
If the battery is drained, it may enter low-voltage protection mode, preventing it from charging. In this case, you would need to use a 29.4V charger with a CC-CV mode to recharge the battery to full capacity.
How to Prevent Battery Depletion
To avoid battery depletion, it is essential to consider the power consumption of all components in the design process, ensuring that the battery maintains sufficient charge during shipping and prolonging its overall lifespan.
Himax is committed to providing thoughtful and feasible custom battery solutions to meet the diverse needs of our customers. If you have custom battery requirements, feel free to contact us to discuss the best battery design solutions for you.