Introduction
When it comes to bulk purchasing custom battery packs, quality and stability are paramount. Whether you’re in the electric vehicle (EV) sector, renewable energy storage, or any other high-demand industry, ordering the right custom lithium-ion battery packs can be a complex process. Choosing a reliable supplier and understanding the critical factors that influence battery quality will ensure that your products perform optimally and last for their intended lifespan.
This blog will provide a comprehensive guide to understanding the custom lithium-ion battery manufacturing process, ensuring that you choose the right supplier and take the necessary steps to secure high-quality, stable battery packs for your needs.
SEO Keywords: Custom battery packs, lithium-ion battery manufacturing, battery quality control, battery testing, battery pack production, bulk battery procurement, quality assurance.
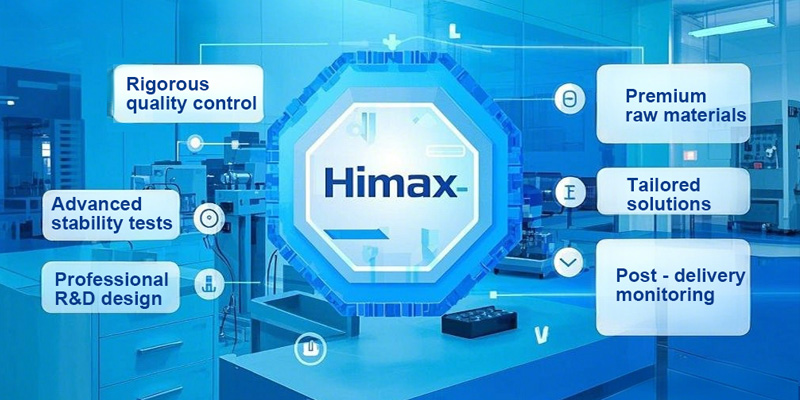
1. Understanding the Lithium-ion Battery Manufacturing Process
To ensure that your custom battery packs meet high standards of quality and stability, it’s essential to have a basic understanding of the lithium-ion battery manufacturing process. Let’s break it down into key steps:
A. Battery Cell Manufacturing
The quality of the battery begins with the raw materials used in the cell construction. Battery cells are composed of several components, including the cathode (typically lithium cobalt oxide or lithium iron phosphate) and the anode (usually graphite or silicon composites). These components must be sourced carefully to ensure optimal performance and safety.
- Electrode Fabrication: The cathode and anode materials are coated onto thin metal foils. This process must be precise, as even slight variations in coating thickness can affect battery performance.
- Cell Assembly: Cells are assembled either in a cylindrical, prismatic, or pouch configuration, depending on the final battery pack design. Each type of cell offers its own advantages in terms of energy density and cost.
B. Electrolyte Filling and Sealing
- Electrolyte Preparation: After the electrodes are assembled, an electrolyte is added to the cell. The electrolyte is the medium that allows ions to move between the cathode and anode during charging and discharging, making it essential for the battery’s function.
- Sealing: Cells are sealed to prevent leakage. This sealing process is critical for battery stability and safety, especially since leaks can lead to performance issues or safety risks such as short circuits or fires.
C. Formation and Initial Testing
Once the cells are fully assembled and sealed, they undergo a formation process, which involves charging and discharging them for the first time. This step activates the cells and helps them reach their full potential.
- Quality Checks: During formation, cells are tested for key parameters like capacity, voltage, and internal resistance. Any deviation from the expected standards should be flagged immediately to prevent poor-quality cells from entering the final product.
D. Final Assembly of Custom Battery Packs
After the individual cells are tested, they are combined into battery packs according to the required configuration, whether it’s series or parallel. The packs also undergo a series of tests to ensure they meet customer specifications.
- Battery Management System (BMS): A BMS is integrated into the pack to monitor and manage the cells’ performance, ensuring safe operation. The BMS regulates temperature, voltage, and current, balancing the charge and protecting the battery from damage.
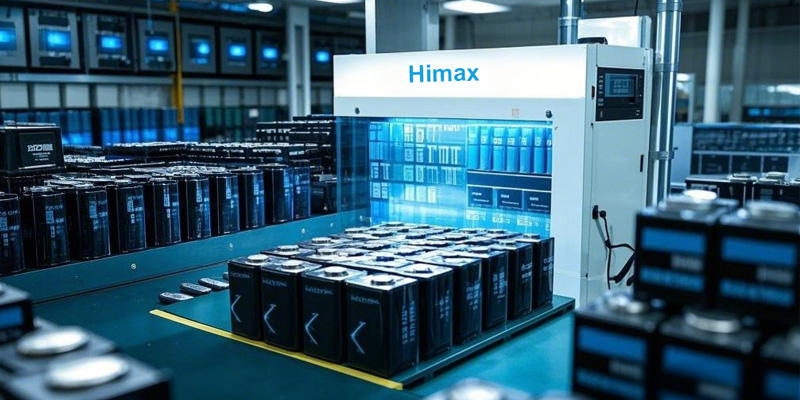
2. Key Factors to Ensure Quality and Stability in Custom Battery Packs
Ensuring the quality and stability of custom battery packs during bulk orders involves considering several critical factors. Below are the most essential elements to watch for:
A. Material Sourcing and Supplier Quality
The quality of the raw materials used in the production of lithium-ion battery cells is foundational to the overall quality of the battery pack.
- Material Quality: Ensure that the battery supplier uses high-quality raw materials such as certified lithium salts, graphite, and quality electrolytes. These materials will directly impact battery performance, lifespan, and safety.
- Supplier Audits and Certifications: Work with suppliers who are certified by recognized standards like ISO 9001, which ensures consistent quality control throughout the manufacturing process. Additionally, certifications such as CE, UL, or IEC-62619 indicate compliance with international safety and performance standards.
B. Precision in Cell Manufacturing
The precision of the cell manufacturing process is crucial for ensuring that the battery pack performs as expected.
- Manufacturing Consistency: Each battery cell should have uniform properties such as capacity, voltage, and internal resistance. Inconsistencies between cells can lead to poor battery performance and even safety risks.
- Automation vs. Manual Labor: Automated production lines generally offer more consistent results, minimizing the risk of human error. Automation ensures precision in the electrode coating, cell assembly, and sealing processes.
C. Effective Battery Testing Protocols
Rigorous testing throughout the manufacturing process is essential to guarantee that custom battery packs meet performance standards and remain stable over time.
- Cycle Life Testing: One of the most important tests is assessing the battery’s cycle life—how many charge/discharge cycles the battery can undergo before its performance starts to degrade. High-quality custom battery packs should withstand 1,000-3,000 cycles, depending on the chemistry used.
- Environmental Stress Testing: Testing the battery under different environmental conditions such as extreme temperatures (hot and cold) is essential. This helps verify the pack’s stability and performance under real-world operating conditions.
- Capacity and Voltage Testing: The battery should meet the exact voltage and capacity specifications required. Any deviation could mean underperformance, leading to customer dissatisfaction.
D. Integration of the Battery Management System (BMS)
A BMS plays a critical role in monitoring and managing the performance of the battery pack.
- BMS Integration: A properly designed BMS prevents issues like overcharging, overheating, and overdischarge, all of which can damage the cells. The BMS also helps to balance the charge between cells, ensuring optimal performance and preventing individual cells from becoming damaged.
- Customization of BMS: Depending on the application, the BMS can be customized to meet the specific needs of your project, whether it’s for energy storage, electric vehicles, or consumer electronics.
3. Quality Control and Testing for Custom Battery Packs
Ensuring that each battery pack meets the highest quality standards is vital to preventing defects and performance issues. Here are key testing and quality control measures to look for:
A. In-Process Inspections
- Visual Inspections: Regular visual checks are performed at various stages of the manufacturing process to identify defects such as torn separators, leaks, or contamination.
- Dimensional Checks: Ensuring that all components (cells, wires, connectors) fit precisely into the final battery pack design is essential for maintaining consistent performance.
B. Functional Testing
- Cycle Life Testing: After production, the battery packs should undergo extensive cycle life testing to simulate their long-term use and evaluate performance consistency over time.
- Stress Testing: Simulate real-world conditions by subjecting the packs to extreme temperatures and varying charge/discharge loads. This will help assess the battery’s durability and reliability in challenging environments.
C. Final Quality Assurance
- End-of-Line Testing: Before shipment, every custom battery pack should undergo final testing, including checks for voltage, capacity, leakage, and any potential safety issues.
- Packaging and Shipping: Proper packaging is critical to avoid damage during transportation. Ensure the supplier follows international safety regulations for lithium-ion batteries to prevent accidents during shipping.
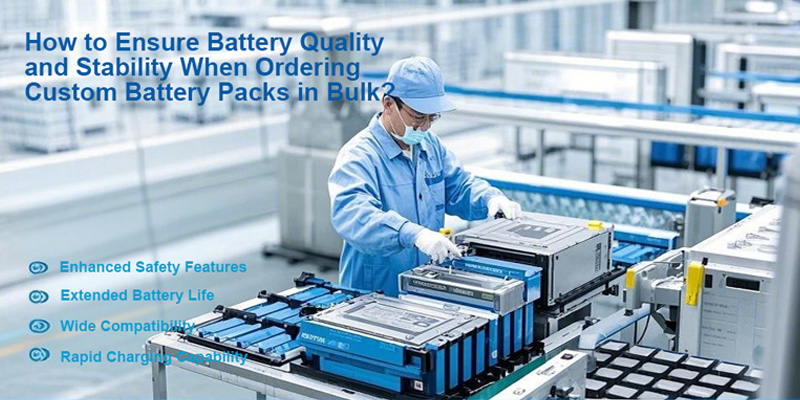
4. Compliance with Safety and Industry Standards
Compliance with safety and industry standards is a key factor in ensuring the quality and stability of custom battery packs.
A. Industry Certifications
- CE & UL Certification: Ensure that the battery packs meet international safety standards such as CE (Conformité Européenne) and UL (Underwriters Laboratories).
- IEC 62619 and RoHS Compliance: These certifications ensure that the batteries meet specific performance, safety, and environmental standards. RoHS ensures that the batteries are free from harmful substances, while IEC 62619 addresses the battery’s safety requirements.
B. Shipping and Handling Compliance
- Dangerous Goods Regulations: Lithium-ion batteries are classified as dangerous goods for transportation. Ensure your supplier complies with regulations such as IATA, IMDG, and DOT to ensure safe shipping.
5. Conclusion: Ensuring High-Quality Custom Battery Packs for Your Business
Ordering custom lithium-ion battery packs in bulk involves careful planning and attention to detail. Understanding the manufacturing process, material sourcing, testing protocols, and quality control measures will help ensure that you receive a high-quality product. By partnering with a trusted supplier who follows rigorous manufacturing standards, you can ensure that your custom battery packs are stable, reliable, and ready for their intended use.
At Himax Battery, we specialize in manufacturing custom lithium-ion battery packs that meet the highest industry standards. With our advanced production processes and comprehensive quality control measures, we guarantee that every product we deliver will perform at its best.